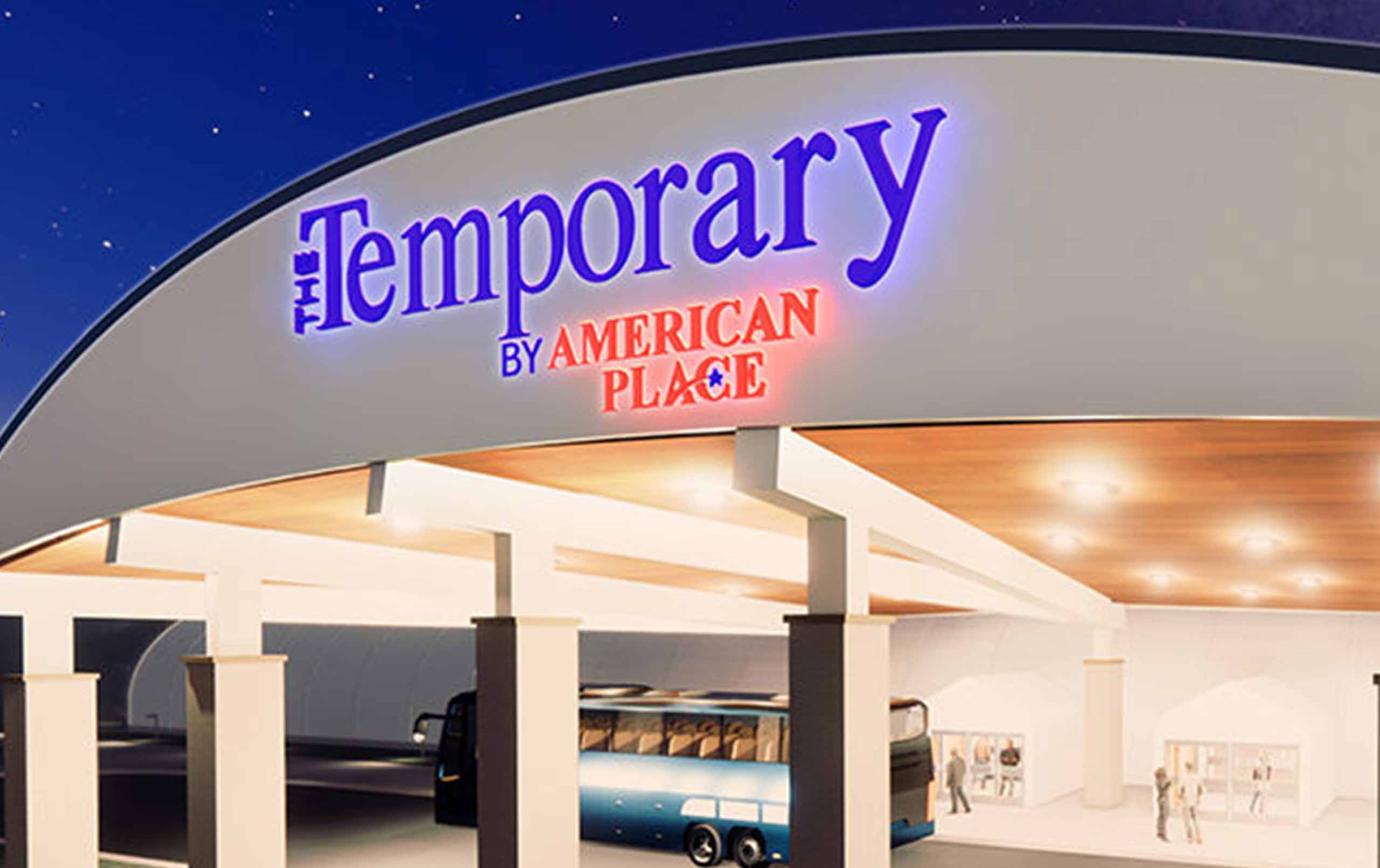
Beat the odds by working the supply chain: architectural team offers tips on accelerating design and construction through a case study of a project that goes from a blank page to a new Waukegan, Illinois temporary casino in less than 12 months.
By April Maifield
A recent Engineering News-Record editorial suggests that 2022 will endure continued supply chain unpredictability, material cost increases, and workforce deficiencies while consumers and employees seek out projects that promote sustainability and equity. Supply chain disruptions impact project budgets and construction schedules, resulting in delays to staff hiring, training, and facility openings.
Here we will explore Legat Architects’ and Turner Construction Companies’ efforts to design and build The Temporary by American Place, a 92,500-square-foot casino in Waukegan, Illinois, within one year.
A Sprint to Start a Marathon
In December 2021, the Illinois Gaming Board selected Full House Resorts, Inc.’s winning bid for a new casino in Waukegan, which is the largest city in and the county seat of Lake County, Illinois’ northeastern-most county.
The accelerated delivery of The Temporary will create jobs, generate tax revenues, and build player excitement ahead of the design and construction of the permanent American Place structure.
The site was previously home to Lakehurst Mall, which operated from 1971 until the final anchor tenant, Carson’s, closed in January 2004. The ensuing demolition of the building resulted in a grass field for the next 18 years.
Full House Resorts started site planning for the temporary facility in December 2021, then brought on Legat in February 2022 based on the firm’s reputation for completing rapid and unique projects. The owner sourced each structure for The Temporary from separate vendors. The membrane structure and diner are owned, while the commercial kitchen and staff trailers are leased. Plans call for the facility to be organized as follows:
- Membrane structure (68,900 square feet): gaming, dining, operations
- Kitchen trailers (7,900 square feet): commercial kitchen
- Staff trailers (12,700 square feet): administrative, employee offices, and support areas
- Diner (3,000 square feet): restaurant
Full House Resorts sourced the procurement of the prefabricated assemblies prior to Legat starting on the project. Part of the larger challenge was how to make all the assemblies work together and determine what else they may need to function. Each of the prefabricated assemblies did get updated in some way during the design process to accommodate utilities systems or local code requirements. The goal with any change during an expedited schedule project is to analyze, adjust, and pivot quickly. It is not personal — it’s simply business.
Early site planning located the temporary and permanent casino structures to allow for concurrent construction activities. The Illinois Gaming Board’s overall opening schedule began with the approval to start The Temporary’s construction in May 2022. To deliver the permanent American Place by 2025, construction activities will be nearly continuous between the two structures.
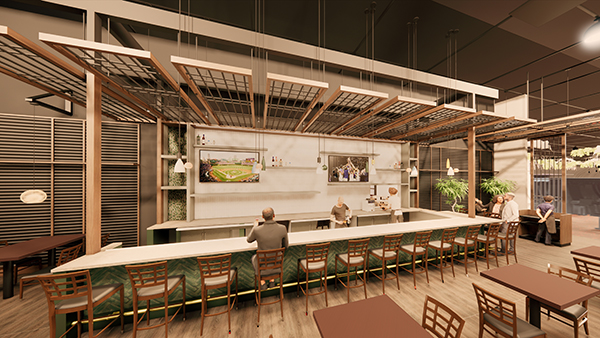
Finding the Shoe That Fits
The Temporary’s membrane structure requires a large footprint with a short construction schedule. The 140-foot by 500-foot footprint gives the most flexibility for the initial layouts and allows for future updates to the gaming equipment positions. Delivery of membrane materials started on June 6, 2022 and plans call for completion of the structure by the end of July when the interior build-out begins.
To speed installation, the owner tasked different vendors with (off-site) prefabrication of kitchen trailers, staff trailers, and the diner. Finished floors of the kitchen and staff trailers are constructed 30 to 36 inches grade, requiring unique site and foundation details so that all finished floor heights are aligned to the membrane structure. The diner’s built-in concrete floor simplifies its foundation installation on site. Prefabricated trailers offer a sustainable benefit of reuse from prior installations through trailer renovation. Moreover, a short mobilization period on-site saves construction time.
Legat created one set of drawings including the vendors’ drawing sets, along with Legat’s custom interior build-out within the membrane structure. The team daily coordinates code compliance, utility systems, and connections between structures to track all the moving parts and vendor requirements.
Turner Construction Companies’ erector will assemble the membrane structure on-site, while the other vendors will set the trailers in place on foundations constructed by Turner.
Contact us to learn more or comment below to share your thoughts on this post.